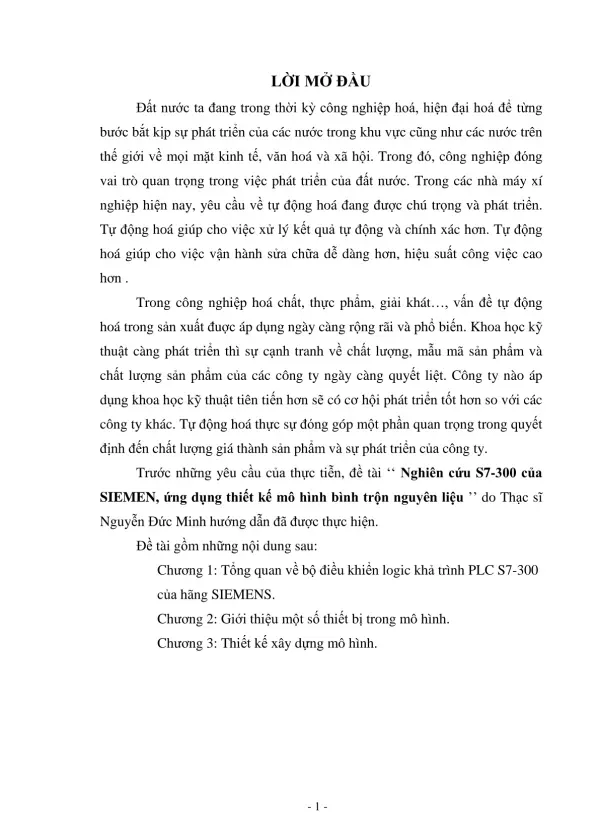
PLC S7-300 Siemens: Mô hình trộn
Thông tin tài liệu
Ngôn ngữ | Vietnamese |
Định dạng | |
Dung lượng | 857.59 KB |
instructor | Thạc sĩ Nguyễn Đức Minh |
Loại tài liệu | Đề tài |
Tóm tắt
I.Vai trò của Tự động hóa trong Công nghiệp
Bài viết nhấn mạnh tầm quan trọng của tự động hóa trong các ngành công nghiệp hiện đại như hóa chất, thực phẩm và đồ uống. Việc áp dụng PLC (Programmable Logic Controller) và các cảm biến tiên tiến giúp nâng cao hiệu suất, độ chính xác, và giảm thiểu chi phí sản xuất. Sự cạnh tranh ngày càng khốc liệt đòi hỏi các công ty phải ứng dụng khoa học kỹ thuật tiên tiến, trong đó tự động hóa đóng vai trò then chốt trong việc quyết định chất lượng và giá thành sản phẩm.
1. Ưu điểm của tự động hóa trong sản xuất
Đoạn văn đầu tiên nhấn mạnh những lợi ích to lớn mà tự động hóa mang lại cho quy trình sản xuất. Cụ thể, tự động hóa giúp xử lý kết quả một cách chính xác và tự động hơn, đơn giản hóa quá trình vận hành và bảo trì, đồng thời gia tăng đáng kể hiệu suất công việc. Điều này được minh chứng qua việc ứng dụng ngày càng rộng rãi của tự động hóa trong nhiều ngành công nghiệp, đặc biệt là hóa chất, thực phẩm và đồ uống. Sự cạnh tranh khốc liệt về chất lượng, mẫu mã và giá thành sản phẩm thúc đẩy các doanh nghiệp tích cực ứng dụng tự động hóa nhằm tối ưu hóa sản xuất và nâng cao khả năng cạnh tranh trên thị trường. Tự động hóa không chỉ góp phần cải thiện chất lượng sản phẩm mà còn là yếu tố quyết định trong việc giảm giá thành và thúc đẩy sự phát triển bền vững của doanh nghiệp. Do đó, việc đầu tư vào tự động hóa là một chiến lược quan trọng để các công ty duy trì vị thế cạnh tranh và đạt được sự tăng trưởng trong bối cảnh thị trường ngày càng toàn cầu hóa và năng động.
2. Xu hướng tự động hóa trong bối cảnh công nghiệp hóa hiện đại hóa đất nước
Phần mở đầu đề cập đến bối cảnh công nghiệp hóa, hiện đại hóa của đất nước, trong đó công nghiệp đóng vai trò quan trọng trong sự phát triển kinh tế - xã hội. Yêu cầu về tự động hóa trong các nhà máy và xí nghiệp ngày càng được chú trọng và phát triển mạnh mẽ. Đây là một xu hướng tất yếu để Việt Nam bắt kịp sự phát triển của các nước trong khu vực và trên thế giới. Việc tích cực ứng dụng công nghệ tự động hóa không chỉ giúp nâng cao năng suất lao động, giảm thiểu rủi ro trong môi trường làm việc nguy hiểm mà còn góp phần quan trọng trong việc hiện đại hóa nền kinh tế quốc gia. Sự chuyển đổi này đòi hỏi sự đầu tư mạnh mẽ vào công nghệ, đào tạo nguồn nhân lực chất lượng cao và sự hỗ trợ từ chính sách của nhà nước. Tự động hóa trở thành một động lực quan trọng để thúc đẩy tăng trưởng kinh tế bền vững và nâng cao vị thế quốc tế của Việt Nam trong bối cảnh hội nhập toàn cầu.
II.Giới thiệu về PLC và các thành phần chính
Phần này tập trung vào PLC, đặc biệt là PLC S7-300 của Siemens, một thiết bị điều khiển logic khả trình phổ biến. PLC cho phép điều khiển linh hoạt các quá trình thông qua lập trình, thay thế cho các mạch điều khiển cứng nhắc. Các thành phần chính của một hệ thống PLC bao gồm bộ xử lý (CPU), bộ nhớ, bộ nguồn, giao diện vào/ra và thiết bị lập trình. Thời gian quét của PLC là một chỉ số quan trọng ảnh hưởng đến hiệu quả điều khiển.
1. PLC Thiết bị điều khiển logic khả trình
Phần này giới thiệu về PLC (Programmable Logic Controller), một thiết bị điều khiển logic khả trình. PLC được mô tả là một bộ điều khiển nhỏ gọn, linh hoạt, cho phép điều khiển các thuật toán số thông qua ngôn ngữ lập trình. Điều này khác biệt so với các mạch điều khiển cứng nhắc truyền thống, cho phép dễ dàng thay đổi thuật toán và trao đổi thông tin với môi trường xung quanh (các PLC khác, máy tính). PLC thực hiện tính toán và soạn thảo các lệnh điều khiển đến các địa chỉ thích hợp. Sự ra đời của PLC, đặc biệt là sau sự cải tiến và phát triển liên tục, đã giải quyết được nhiều vấn đề của các hệ thống điều khiển truyền thống, đáp ứng nhu cầu của công nghiệp hiện đại. Một hệ thống điều khiển ưu việt cần có tính tự động cao, kích thước nhỏ gọn, giá thành thấp, dễ thi công, sửa chữa và vận hành linh hoạt. PLC đáp ứng đầy đủ các yêu cầu này.
2. Thành phần cơ bản của một bộ PLC
Một hệ thống PLC thông dụng thường bao gồm năm bộ phận chính: bộ xử lý trung tâm (CPU), bộ nhớ, bộ nguồn, giao diện vào/ra và thiết bị lập trình. CPU, hay bộ xử lý trung tâm, là linh kiện chứa bộ vi xử lý, nhận tín hiệu vào, thực hiện các hoạt động điều khiển theo chương trình được lưu trữ trong bộ nhớ, và truyền các quyết định dưới dạng tín hiệu đến các thiết bị ra. Thời gian quét của chương trình (thường được đo trên chương trình 1 Kbyte) dùng để đánh giá thời gian trễ của PLC. Thời gian quét dài có thể gây trở ngại cho quá trình điều khiển, đòi hỏi các biện pháp đặc biệt như lặp lại các lệnh quan trọng hoặc điều khiển thông tin chuyển giao để loại bỏ các lệnh ít quan trọng. Nếu các biện pháp này không hiệu quả, cần sử dụng PLC có thời gian quét ngắn hơn. Giao diện vào/ra cho phép PLC nhận thông tin từ các thiết bị ngoại vi (công tắc, cảm biến,…) và cung cấp tín hiệu ra cho các thiết bị khác (cuộn dây contactor, rơle, van điện từ,…). Các tín hiệu có thể là rời rạc, liên tục hoặc logic. Bộ nhớ lưu trữ chương trình điều khiển và dữ liệu, có thể được thiết kế thành module để dễ dàng mở rộng.
III.Mô đun của PLC S7 300 và ứng dụng
Phần này đi sâu vào cấu trúc mô đun của PLC S7-300. Khả năng mở rộng mô đun vào/ra, cùng với các ngôn ngữ lập trình như LAD, FBD và STL, làm cho PLC S7-300 thích hợp cho nhiều ứng dụng khác nhau. Các mô đun CPU, cùng với các mô đun chức năng chuyên dụng (IFM), cho phép tùy chỉnh hệ thống để đáp ứng nhu cầu cụ thể của từng bài toán điều khiển. Việc lựa chọn các mô đun phù hợp là rất quan trọng để tối ưu hóa hệ thống.
1. Giới thiệu chung về PLC S7 300 của Siemens
Phần này tập trung giới thiệu PLC S7-300 của hãng Siemens, một trong những loại PLC phổ biến hiện nay. Trước khi có PLC, việc điều khiển các dây chuyền sản xuất thường dựa trên việc kết nối các linh kiện riêng lẻ (rơle, timer, contactor...), dẫn đến hệ thống cồng kềnh, khó bảo trì và năng suất thấp. PLC S7-300 ra đời như một giải pháp tối ưu, khắc phục những nhược điểm trên. PLC S7-300 được đánh giá cao nhờ tính tự động hóa cao, kích thước nhỏ gọn, giá thành hợp lý, dễ thi công và bảo trì, cùng chất lượng hoạt động ổn định và linh hoạt. Các ưu điểm chính của PLC bao gồm khả năng thay đổi thuật toán điều khiển dễ dàng, mở rộng mô-đun vào/ra khi cần thiết, ngôn ngữ lập trình dễ hiểu, và khả năng truyền thông với nhiều thiết bị khác nhau (máy tính, các PLC khác, thiết bị giám sát...). PLC hoạt động dựa trên nguyên lý của một máy tính với bộ vi xử lý (CPU), hệ điều hành, bộ nhớ lưu trữ chương trình và dữ liệu, cũng như các cổng vào/ra để trao đổi thông tin với môi trường bên ngoài. Ngoài ra, PLC còn tích hợp các bộ định thời (Timer), bộ đếm (Counter) và nhiều hàm chuyên dụng khác, tạo nên một bộ điều khiển linh hoạt và hiệu quả.
2. Các mô đun của PLC S7 300 và cấu trúc
Phần này đề cập đến các mô-đun của PLC S7-300. Cấu hình của PLC S7-300 không cố định, tùy thuộc vào yêu cầu của từng bài toán điều khiển. Tuy nhiên, tối thiểu phải có mô-đun nguồn nuôi và mô-đun CPU. Các mô-đun khác, như mô-đun truyền nhận tín hiệu với môi trường bên ngoài và các mô-đun chức năng chuyên dụng (PID, điều khiển mờ, điều khiển động cơ bước, truyền thông...), được gắn trên một thanh Rack. Các mô-đun sử dụng chung một bộ vi xử lý nhưng khác nhau về cổng vào/ra onboard và các khối hàm đặc biệt tích hợp sẵn (IFM – Integrated Function Module), ví dụ như CPU312 IFM, CPU314 IFM. Mô-đun CPU chứa bộ vi xử lý, hệ điều hành, bộ nhớ, bộ định thời, bộ đếm, cổng truyền thông (RS485), và có thể có thêm một số cổng vào/ra số (onboard). Vùng nhớ của CPU được chia thành các miền khác nhau, bao gồm miền dữ liệu đầu vào (I), miền biến cờ (M), miền bộ định thời (T), miền dữ liệu địa phương (L), và miền dữ liệu khối (DB). Mỗi miền có chức năng và cách truy cập riêng, cho phép lập trình viên tổ chức và quản lý dữ liệu một cách hiệu quả.
3. Khái niệm về thời gian quét và cấu trúc chương trình
Một khía cạnh quan trọng được đề cập là thời gian quét (Scan Time) – thời gian PLC thực hiện một vòng quét chương trình. Thời gian này không cố định và phụ thuộc vào số lượng lệnh, khối lượng dữ liệu truyền thông, và các tín hiệu ngắt. Các lệnh vào/ra thường được thực hiện thông qua bộ đệm ảo trong vùng nhớ, chỉ truy cập trực tiếp cổng vật lý khi cần thiết. Chương trình xử lý ngắt (ví dụ OB40, OB80) được thực hiện trong vòng quét khi xuất hiện tín hiệu ngắt, có thể làm tăng thời gian quét. Cấu trúc chương trình có thể tuyến tính (phù hợp với bài toán nhỏ, đơn giản, sử dụng khối OB1) hoặc có cấu trúc với các khối hàm chức năng (FB), khối chức năng (FC), và khối dữ liệu (DB). FB có khả năng trao đổi dữ liệu với các khối khác thông qua DB. DB có hai loại: Shared DB và Instance DB. PLC S7-300 cho phép gọi chương trình con lồng nhau, nhưng số lần gọi bị giới hạn tùy thuộc vào loại mô-đun CPU. Vượt quá giới hạn này sẽ dẫn đến lỗi và PLC dừng hoạt động. Khối SDB (System Data Block) lưu trữ dữ liệu cấu hình và thông tin toàn cục được chia sẻ giữa các CPU.
IV.Thiết kế và hoạt động của cảm biến mức
Một phần quan trọng của bài viết là mô tả thiết kế và nguyên lý hoạt động của một cảm biến mức tự chế tạo. Cảm biến này được sử dụng trong mô hình hệ thống trộn nhiên liệu, cho thấy ứng dụng thực tế của cảm biến trong tự động hóa. So sánh với các sản phẩm thương mại như cảm biến tiệm cận của AUTONIC và bộ điều khiển của OMRON, cảm biến mức tự chế tạo này có chi phí thấp hơn mà vẫn đảm bảo hiệu quả hoạt động.
1. Giới thiệu chung về cảm biến và tầm quan trọng
Phần này mở đầu bằng việc giới thiệu khái niệm cảm biến như một thiết bị chuyển đổi các đại lượng vật lý (không mang tính chất điện) thành các đại lượng điện có thể đo được. Cảm biến đóng vai trò quan trọng trong hệ thống đo lường và điều khiển tự động. Mặc dù đã được sử dụng từ lâu, nhưng chỉ trong vài thập kỷ gần đây, cảm biến mới thực sự thể hiện vai trò quan trọng trong kỹ thuật và công nghiệp, đặc biệt trong lĩnh vực đo lường, kiểm tra và điều khiển tự động. Sự phát triển của khoa học và công nghệ trong lĩnh vực vật liệu, điện tử và tin học đã giúp giảm kích thước, cải thiện chức năng và mở rộng phạm vi ứng dụng của cảm biến. Hiện nay, cảm biến được ứng dụng rộng rãi trong nhiều lĩnh vực, từ hệ thống tự động phức tạp, robot, kiểm tra chất lượng sản phẩm, tiết kiệm năng lượng, bảo vệ môi trường đến giao thông vận tải, sản xuất hàng tiêu dùng, bảo quản thực phẩm và sản xuất ô tô. Việc trang bị kiến thức về cảm biến là rất cần thiết cho các kỹ sư và cán bộ kỹ thuật.
2. Thiết kế và nguyên lý hoạt động của cảm biến mức tự chế
Phần này tập trung vào thiết kế và nguyên lý hoạt động của một cảm biến mức tự chế tạo. Tác giả đã nghiên cứu nguyên lý hoạt động của cảm biến mức sau khi tham khảo các sản phẩm thương mại như bộ điều khiển kiểm tra mức 61F của OMRON và cảm biến tiệm cận loại điện dung của AUTONIC, nhận thấy giá thành của các sản phẩm này khá cao. Cảm biến mức tự chế tạo hoạt động dựa trên việc sử dụng rơle và transistor. Ban đầu, khi cấp điện 12VDC vào cuộn hút của rơle, rơle không đóng do transistor C828 không dẫn. Rơle chỉ dẫn khi chân COM được kết nối với một trong các chân Mức1, Mức2, Mức3, làm cho transistor C828 dẫn và dòng điện chạy qua cuộn hút của rơle RL1 (hoặc RL2, RL3 tương ứng), đóng tiếp điểm thường mở và đưa tín hiệu vào đầu vào của PLC. Cảm biến này hoạt động ổn định và có giá thành thấp hơn nhiều so với các cảm biến công nghiệp. Mô tả mạch nguồn ổn áp cũng được đưa ra, bao gồm biến áp giảm áp, cầu chỉnh lưu, và IC ổn áp (IC7824 và IC7812) để tạo ra điện áp một chiều ổn định cung cấp cho cảm biến.
V.Mô hình hệ thống trộn nhiên liệu tự động
Bài viết trình bày một mô hình hệ thống trộn nhiên liệu tự động sử dụng PLC S7-300 và cảm biến mức. Hệ thống bao gồm các thành phần chính: khối nút nhấn (Start, Stop, Emergency), khối điều khiển (PLC S7-300), các van điện từ, động cơ trộn, và cảm biến. Mô hình này minh họa cách thức tự động hóa được áp dụng để tối ưu hóa quá trình trộn nhiên liệu, với khả năng kiểm soát mức nhiên liệu, điều khiển van và động cơ một cách chính xác.
1. Mục tiêu và cấu trúc mô hình
Mục tiêu của đồ án là thiết kế mô hình hệ thống trộn nhiên liệu tự động, sử dụng PLC S7-300 và cảm biến mức. Hệ thống được thiết kế để hoạt động thông minh, hiệu quả và tối ưu. Mô hình bao gồm ba khối chính: Khối nút nhấn với các nút Start, Stop và Emergency để điều khiển hệ thống, cho phép bắt đầu, dừng chu trình hoặc dừng khẩn cấp trong trường hợp sự cố. Khối điều khiển trung tâm là PLC S7-300, nhận tín hiệu từ các nút nhấn và cảm biến mức, xử lý thông tin và đưa ra tín hiệu điều khiển cho các van và động cơ. Các thành phần khác bao gồm các van cấp nhiên liệu (A và B), van xả, động cơ trộn nhiên liệu và cảm biến mức (được chế tạo trong đồ án). Hệ thống tự động hóa này nhằm tối ưu hóa quá trình trộn nhiên liệu, đảm bảo hiệu quả và độ chính xác cao hơn so với các phương pháp truyền thống.
2. Nguyên lý hoạt động của hệ thống
Nguyên lý hoạt động của hệ thống trộn nhiên liệu tự động như sau: Khi hệ thống được kích hoạt (bằng nút Start), PLC S7-300 đầu tiên kiểm tra mức nhiên liệu trong bình bằng cảm biến mức. Nếu nhiên liệu còn (ở mức 1), van xả mở để xả hết nhiên liệu cũ. Nếu không còn nhiên liệu, van cấp A mở để cấp nhiên liệu vào bình đến mức 2 (mức đặt trước), sau đó đóng van A và mở van B để tiếp tục cấp nhiên liệu đến mức 3 (mức đầy). Khi đạt mức 3, van B đóng và động cơ trộn bắt đầu hoạt động trong 30 giây. Sau khi động cơ ngừng, van xả mở để xả nhiên liệu xuống mức 1, sau đó đóng van xả và chu trình lại bắt đầu với van cấp A. Toàn bộ quá trình được điều khiển bởi PLC S7-300 dựa trên tín hiệu từ các cảm biến mức và các nút nhấn. Hệ thống sử dụng cảm biến mức tự chế tạo, có khả năng dễ dàng thay đổi mức, giúp tối ưu hóa quá trình điều khiển.
3. Hạn chế của mô hình
Mặc dù mô hình hệ thống trộn nhiên liệu đã được chế tạo thành công và hoạt động ổn định, nhưng vẫn còn một số hạn chế cần được cải thiện trong các phiên bản tiếp theo. Việc sử dụng van điện từ làm cho tốc độ cấp và xả nhiên liệu bị chậm. Đây là một điểm cần được khắc phục để nâng cao hiệu quả của hệ thống. Bên cạnh đó, chương trình điều khiển trên PLC S7-300 vẫn chưa được tối ưu hoàn toàn. Có thể có những cải tiến về thuật toán để giảm thời gian chu trình, tăng tốc độ phản hồi và độ chính xác của hệ thống. Việc nghiên cứu và tối ưu hóa chương trình điều khiển sẽ là một hướng phát triển quan trọng để nâng cao hiệu suất và độ tin cậy của hệ thống trộn nhiên liệu tự động này.