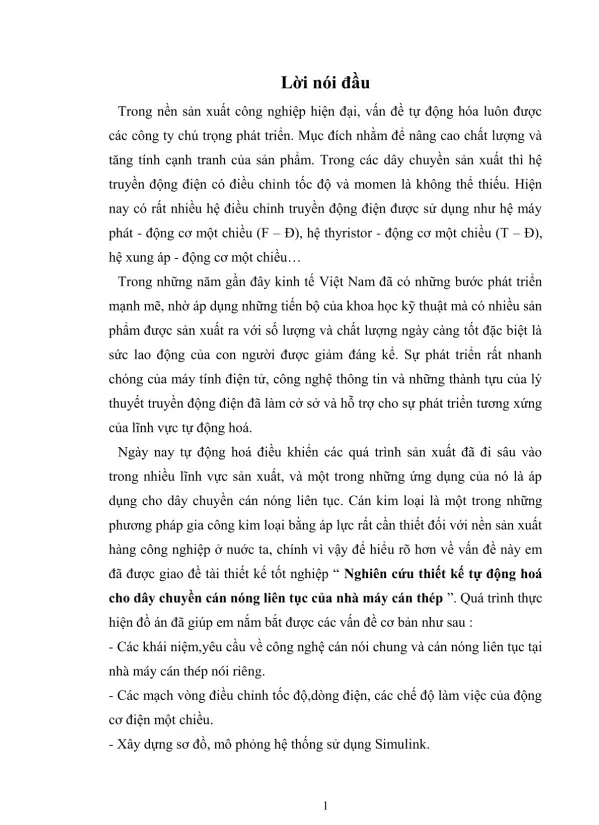
Tự động hóa dây chuyền cán nóng
Thông tin tài liệu
Chuyên ngành | Kỹ thuật điện |
Đơn vị | Nhà máy cán thép Việt-Nhật |
Loại tài liệu | Đồ án tốt nghiệp |
Ngôn ngữ | Vietnamese |
Định dạng | |
Dung lượng | 2.25 MB |
Tóm tắt
I.Tổng quan về Hệ thống Cán Nóng Liên tục và Tự động hóa
Đề tài nghiên cứu thiết kế tự động hóa dây chuyền cán nóng liên tục (CNLT) tại một nhà máy cán thép tập trung vào việc tối ưu hóa quá trình sản xuất thép. Việc tự động hóa này nhắm đến việc nâng cao chất lượng sản phẩm, tăng tính cạnh tranh, và giảm thiểu sức lao động. Hệ thống sử dụng rộng rãi hệ thống truyền động điện, đặc biệt là động cơ một chiều, được điều khiển bởi các biến tần và PLC để đảm bảo chính xác và hiệu quả trong quá trình cán. Các thành phần quan trọng bao gồm hệ thống nạp phôi, lò nung liên tục, hệ thống giá cán (bao gồm cả giá cán thô, trung và tinh), hệ thống làm nguội, và hệ thống cắt và đóng bó thành phẩm. Nhà máy sử dụng thiết bị của hãng Siemens, bao gồm các bộ biến đổi Simoreg 6RA70, để điều khiển chính xác các động cơ và hệ thống. Quá trình sản xuất thép liên tục trải qua nhiều giai đoạn, từ cấp phôi đến sản phẩm hoàn thiện, tất cả đều được tích hợp và điều khiển tự động.
1. Giới thiệu về dây chuyền cán nóng liên tục và tự động hóa
Đoạn văn này giới thiệu tổng quan về việc ứng dụng tự động hóa trong dây chuyền cán nóng liên tục, một phương pháp gia công kim loại bằng áp lực rất quan trọng trong nền công nghiệp hiện nay. Nó nhấn mạnh tầm quan trọng của việc nghiên cứu và thiết kế tự động hóa cho dây chuyền này nhằm nâng cao hiệu quả sản xuất, chất lượng sản phẩm và giảm thiểu sức lao động. Sự phát triển nhanh chóng của công nghệ máy tính, công nghệ thông tin và lý thuyết truyền động điện đã tạo điều kiện thuận lợi cho sự phát triển của lĩnh vực tự động hóa, đặc biệt là trong ngành sản xuất thép. Tự động hóa được xem là yếu tố then chốt để tăng tính cạnh tranh của sản phẩm trên thị trường và đáp ứng nhu cầu ngày càng cao của nền kinh tế. Trong các dây chuyền sản xuất hiện đại, hệ truyền động điện có khả năng điều chỉnh tốc độ và mô-men là một thành phần không thể thiếu, với nhiều hệ thống điều chỉnh khác nhau đang được sử dụng, bao gồm hệ máy phát - động cơ một chiều, hệ thyristor - động cơ một chiều và hệ xung áp - động cơ một chiều. Mục tiêu của việc tự động hóa là nhằm nâng cao chất lượng và tăng tính cạnh tranh của sản phẩm.
2. Quá trình cán nóng liên tục và các giai đoạn chính
Phần này mô tả chi tiết quá trình cán nóng liên tục, bao gồm các giai đoạn chính từ khâu chuẩn bị nguyên liệu đến sản phẩm hoàn thiện. Quá trình bắt đầu từ việc cấp phôi, được vận chuyển bằng hệ thống cầu trục và xe goòng vào nhà máy. Phôi được đặt lên sàn nạp phôi tự động, sử dụng hệ thống cóc gạt và con lăn để di chuyển phôi vào lò nung. Lò nung liên tục, được thiết kế với đáy động và đáy tĩnh, có công suất lớn (55 tấn/giờ), giúp làm nóng phôi đến nhiệt độ cần thiết. Sau khi nung, phôi được đưa vào hệ thống giá cán thô, cán trung và cán tinh, với số lượng giá cán khác nhau tùy thuộc vào loại sản phẩm. Hệ thống giá cán sử dụng động cơ một chiều để điều khiển tốc độ và mô-men, đảm bảo chất lượng sản phẩm. Sau khi cán, sản phẩm được làm nguội bằng không khí hoặc nước áp lực cao trước khi được cắt thành các đoạn theo yêu cầu. Cuối cùng, sản phẩm được đóng bó, cân, gắn nhãn mác và đưa vào kho thành phẩm. Mô tả chi tiết các thiết bị như máy cắt nguội 600T, hệ thống xích tải, máy đóng bó và hệ thống cân tự động cho thấy sự phức tạp và tính tự động hóa cao của dây chuyền sản xuất.
3. Hệ thống truyền động và điều khiển trong dây chuyền cán nóng liên tục
Phần này tập trung vào hệ thống truyền động và điều khiển, nhấn mạnh vào việc sử dụng động cơ một chiều trong các giá cán. Đặc điểm của công nghệ cán đòi hỏi mô-men quán tính lớn và dải điều chỉnh tốc độ rộng, do đó động cơ một chiều kích từ độc lập là lựa chọn phù hợp. Hãng Siemens cung cấp các bộ biến đổi Simoreg để điều khiển động cơ, cho phép thay đổi điện áp đặt vào phần ứng và thay đổi kích từ động cơ, từ đó điều chỉnh tốc độ và mô-men. Ngoài ra, các hệ thống con lăn và máy đẩy tiếp cũng được điều khiển bằng biến tần của Siemens (Simorvert), cho phép thay đổi tần số và điện áp để điều chỉnh tốc độ và mô-men của động cơ. Việc bố trí hợp lý sơ đồ công nghệ đảm bảo chu trình sản xuất hiệu quả, đơn giản và an toàn cho người vận hành. Hệ thống có hai chế độ điều khiển: điều khiển tại chỗ và điều khiển từ xa tại buồng điều khiển trung tâm, mỗi chế độ đều có hai chế độ hoạt động: tự động và thủ công. Buồng điều khiển trung tâm sử dụng các thiết bị cảm biến như photocell, sensor tiệm cận, và camera để giám sát quá trình sản xuất.
II.Hệ thống Điều khiển và Giám sát
Hệ thống tự động hóa được giám sát và điều khiển thông qua một hệ thống điều khiển số hiện đại. Điều khiển có thể thực hiện tại chỗ hoặc từ xa tại buồng điều khiển trung tâm. Các sensor, photocell, và camera cung cấp dữ liệu thời gian thực về trạng thái hoạt động của các thiết bị. Dữ liệu này được hiển thị trên giao diện điều khiển PC, đèn báo, và còi báo động. Hệ thống sử dụng giao thức USS cho phép giao tiếp giữa các bộ biến đổi và thiết bị điều khiển. Bộ biến đổi Simoreg đóng vai trò quan trọng trong việc điều chỉnh tốc độ và mô-men của các động cơ một chiều, đảm bảo sự chính xác và ổn định của toàn bộ dây chuyền cán nóng liên tục.
1. Kiểu điều khiển và vị trí điều khiển
Hệ thống tự động hóa trong dây chuyền cán nóng liên tục cho phép điều khiển cả tại chỗ và từ xa. Điều khiển tại chỗ được thực hiện tại các trạm cục bộ đặt ở từng khu vực trong dây chuyền, cho phép vận hành và giám sát trực tiếp các thiết bị tại điểm đó. Trong khi đó, điều khiển từ xa được thực hiện tập trung tại buồng điều khiển trung tâm, cung cấp khả năng giám sát và điều khiển toàn bộ dây chuyền một cách tổng thể. Điều khiển từ xa cho phép vận hành cả chế độ tự động và thủ công, mang lại sự linh hoạt cao trong quá trình sản xuất. Việc tích hợp cả hai kiểu điều khiển này giúp tối ưu hóa quá trình vận hành, cho phép can thiệp trực tiếp khi cần thiết và giám sát toàn diện từ trung tâm điều khiển.
2. Hệ thống giám sát và thu thập dữ liệu
Buồng điều khiển trung tâm đóng vai trò quan trọng trong việc giám sát và thu thập dữ liệu. Hệ thống sử dụng các thiết bị cảm biến hiện đại, bao gồm photocell quang học, sensor tiệm cận, và các thiết bị phản hồi tốc độ, dòng điện, áp suất và mức vật liệu. Dữ liệu từ các sensor này được truyền về buồng điều khiển trung tâm, cung cấp thông tin chi tiết về trạng thái hoạt động của các thiết bị trong toàn bộ dây chuyền. Ngoài ra, hệ thống camera nhà xưởng được tích hợp để giám sát trực quan quá trình sản xuất. Dữ liệu thu thập được được hiển thị trên giao diện điều khiển PC, cùng với đèn báo và còi báo động để cảnh báo các sự cố hoặc tình huống bất thường. Hệ thống giám sát toàn diện này giúp người vận hành kịp thời phát hiện và xử lý các sự cố, đảm bảo sự vận hành ổn định và an toàn của dây chuyền cán nóng liên tục.
3. Giao thức truyền thông và thiết bị điều khiển
Hệ thống điều khiển sử dụng công nghệ điều khiển số, được đánh giá cao hơn so với mạch điều khiển tương tự nhờ tính mềm dẻo trong việc thay đổi cấu trúc và thông số, độ chính xác cao và khả năng chống nhiễu tốt. Nhà máy sử dụng bộ biến đổi số Simoreg 6RA70 của Siemens để điều khiển hệ thống cán, cho thấy sự ứng dụng công nghệ tiên tiến trong quá trình tự động hóa. Giao thức truyền thông USS được sử dụng để liên kết giữa các bộ biến đổi và thiết bị điều khiển, cho phép trao đổi dữ liệu hiệu quả. Tuy nhiên, giao thức này chỉ hỗ trợ liên kết kiểu Master-Slave, nghĩa là các bộ biến đổi chỉ gửi tín hiệu khi nhận được yêu cầu từ thiết bị điều khiển trung tâm (Master). Việc sử dụng các thiết bị và giao thức hiện đại này đảm bảo tính ổn định, chính xác và hiệu quả của hệ thống điều khiển và giám sát toàn bộ dây chuyền cán nóng liên tục.
III.Điều khiển Động cơ và Tối ưu hóa Quá trình
Việc điều khiển động cơ một chiều trong hệ thống cán nóng liên tục đòi hỏi độ chính xác cao. Mỗi giá cán được trang bị một hoặc nhiều động cơ, được điều khiển bởi các bộ biến đổi Simoreg. Việc điều chỉnh tốc độ và mô-men được thực hiện thông qua các mạch vòng điều chỉnh dòng điện và tốc độ. Động cơ kích từ độc lập được lựa chọn do khả năng điều chỉnh tốc độ rộng và mô-men khởi động lớn. Các phương pháp điều chỉnh đồng bộ tốc độ và mô-men giữa các động cơ được áp dụng để đảm bảo hiệu suất và tránh quá tải. Tối ưu hóa quá trình bao gồm việc điều chỉnh lượng nhiên liệu (khí CO) cho lò nung để giảm tổn hao và bảo vệ môi trường.
1. Điều khiển động cơ một chiều trong hệ thống cán
Trong hệ thống cán nóng liên tục, động cơ một chiều được sử dụng rộng rãi do khả năng điều chỉnh tốc độ và mô-men tốt. Mỗi giá cán thường được trang bị một động cơ riêng biệt, hoặc trong trường hợp cụm giá cán Block, thì sử dụng hai động cơ một chiều kích từ độc lập nối đồng trục. Đặc tính cần thiết của động cơ cho hệ thống cán là mô-men quán tính lớn và dải điều chỉnh tốc độ rộng. Việc điều khiển động cơ được thực hiện thông qua các bộ biến đổi, ví dụ như Simoreg của Siemens, cho phép điều chỉnh điện áp đặt vào phần ứng và thay đổi kích từ để đạt được tốc độ và mô-men mong muốn. Hệ thống con lăn và máy đẩy tiếp cũng được điều khiển bằng biến tần, cho phép thay đổi tần số và điện áp để điều chỉnh tốc độ và mô-men của động cơ. Sự lựa chọn động cơ một chiều là dựa trên ưu điểm về mô-men khởi động lớn, khả năng điều chỉnh tốc độ dễ dàng ở cả hai chiều, cấu trúc mạch đơn giản và chất lượng điều chỉnh cao trong dải điều chỉnh tốc độ rộng.
2. Điều khiển đồng bộ tốc độ và mô men
Để đảm bảo hiệu suất và tránh quá tải cho động cơ, việc điều chỉnh đồng bộ tốc độ và mô-men giữa các động cơ là rất quan trọng. Điều này được thực hiện thông qua hai hệ thống điều chỉnh tự động truyền động điện riêng biệt, với các mạch vòng điều chỉnh dòng điện và tốc độ. Máy phát tốc đo tốc độ dài của dây chuyền, và bộ so sánh so sánh tín hiệu đặt với tốc độ thực tế của động cơ để phát hiện sai lệch. Sai lệch tốc độ này, kết hợp với vận tốc dài, được sử dụng để điều khiển. Một phương pháp điều chỉnh đồng bộ tốc độ là bằng cách thay đổi từ thông và điện áp phần ứng. Trong trường hợp tải thay đổi liên tục, việc điều chỉnh mô-men và công suất của động cơ là cần thiết để đảm bảo hiệu suất làm việc. Điều này thể hiện sự phức tạp và yêu cầu chính xác cao trong việc điều khiển động cơ cho dây chuyền cán nóng liên tục.
3. Tối ưu hóa quá trình và điều khiển lò nung
Tối ưu hóa quá trình cán nóng liên tục bao gồm việc điều chỉnh lượng nhiên liệu cho lò nung. Lò nung sử dụng khí CO, được cung cấp từ một trạm khí hóa than. Việc điều chỉnh lượng khí CO và khí nén giúp tận dụng tối đa nhiên liệu, tránh tổn hao và giảm lượng khí thải ra môi trường. Điều chỉnh chính xác này cũng giúp giảm thiểu tổn hao kim loại do cháy bề mặt phôi. Phôi được di chuyển vào và ra khỏi lò nung bằng hệ thống con lăn tự động và hệ thống tay đẩy. Trong quá trình cán, việc sử dụng máy tạo trùng giúp ổn định phôi, tránh hiện tượng đứt phôi và đảm bảo chất lượng sản phẩm. Các máy cắt tự động được tích hợp để xử lý các trường hợp sự cố hoặc phôi bị lỗi, đảm bảo an toàn và hiệu quả cho toàn bộ quá trình.
IV.Thiết kế và Phối hợp Cơ cấu
Thiết kế tự động hóa cho dây chuyền CNLT chú trọng đến sự phối hợp chính xác giữa các cơ cấu khác nhau. Sơ đồ thời gian được lập trình để đảm bảo hiệu quả và năng suất. Sử dụng xylanh khí nén và các cơ cấu khác để thực hiện các thao tác chính xác, nhanh chóng trong chu trình sản xuất. Các cơ cấu cần được phối hợp chính xác để đảm bảo an toàn và hiệu quả. Mỗi cơ cấu có chức năng cụ thể và cần được điều khiển chính xác thông qua hệ thống PLC.
1. Sơ đồ khối và phối hợp cơ cấu
Tài liệu đề cập đến sơ đồ khối cho phương án thiết kế tự động hóa dây chuyền. Quá trình bắt đầu từ cụm cấp cán, nơi các chi tiết được cấp và định vị trên giá nâng. Giá nâng có chuyển động nâng hạ để di chuyển cụm chi tiết dọc theo dây chuyền. Hệ thống máy cắt nguội và cữ chặn so đầu được sử dụng để cắt đầu đuôi và cắt thép theo chiều dài mong muốn. Máy đếm thép sử dụng cặp Photocell tần số cao, trong khi máy buộc tự động có thể cài đặt số lần buộc, số sợi và tốc độ buộc. Cuối cùng, hệ thống cân và in Eteket sử dụng bốn loadcel để đo trọng lượng và in thông tin lên sản phẩm. Một biểu đồ thời gian phối hợp chuyển động của các cơ cấu được trình bày, cho thấy thời gian hoạt động của các xylanh khí nén (cấp cán, cấp tảm, cấp ruột, vặn tảm, phiến kẹp, chốt tỳ) và cơ cấu di chuyển. Chu kỳ làm việc được thiết kế để đảm bảo năng suất 50 sản phẩm/phút, với chu kỳ 1.2s. Phối hợp giữa các xylanh được điều khiển bởi bộ cam, đảm bảo hoạt động đồng bộ và hiệu quả.
2. Phân tích phối hợp chuyển động và lựa chọn động cơ
Phân tích biểu đồ thời gian cho thấy sự phối hợp chính xác giữa các xylanh. Ví dụ, trong 0.4s đầu, các xylanh cấp cán, ruột, tảm, vặn tảm bắt đầu đẩy ra, và dừng lại ở vị trí làm việc trong khoảng 0.4s-0.5s. Sự phối hợp giữa các xylanh khác nhau được thể hiện rõ ràng, đảm bảo quá trình hoạt động trơn tru. Việc sử dụng phiến kẹp để kẹp chặt cán trên giá đỡ giúp dễ dàng đóng tảm. Động cơ điện một chiều được đánh giá cao hơn các loại động cơ khác do mô-men khởi động lớn, khả năng điều chỉnh tốc độ dễ dàng ở cả hai chiều, cấu trúc mạch đơn giản và chất lượng điều chỉnh cao. Sơ đồ mạch lực thường sử dụng hai bộ chỉnh lưu cầu Thyristor điều khiển hoàn toàn mắc song song ngược, kích từ độc lập, phù hợp cho mọi dải công suất và có tần số đảo chiều lớn. Hệ thống làm việc an toàn và không có dòng điện cân bằng chảy giữa các bộ biến đổi. Nhà máy sử dụng điều khiển số với bộ biến đổi Simoreg 6RA70 của Siemens cho độ chính xác cao và khả năng chống nhiễu tốt.