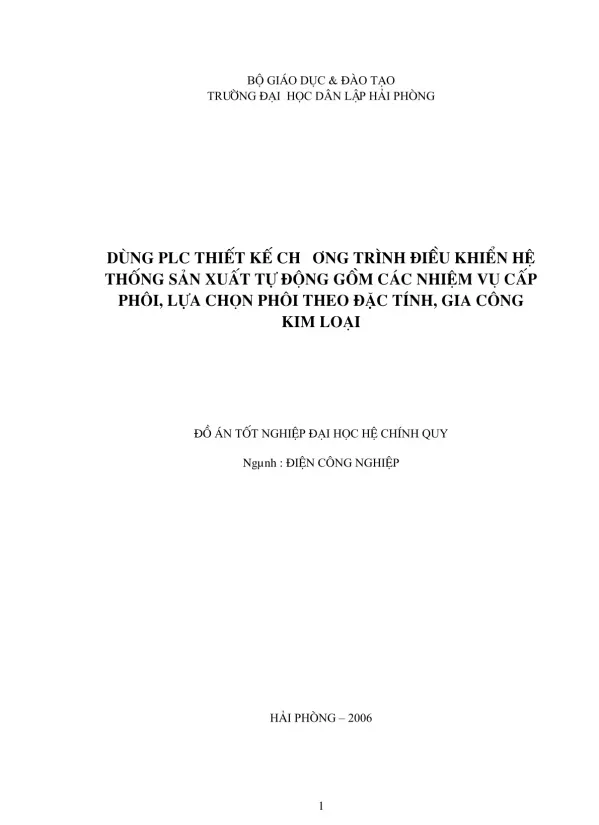
Điều khiển PLC: Tự động hóa sản xuất
Thông tin tài liệu
Trường học | Trường Đại Học Dân Lập Hải Phòng |
Chuyên ngành | Điện Công Nghiệp |
Địa điểm | Hải Phòng |
Loại tài liệu | Đồ án tốt nghiệp đại học hệ chính quy |
Ngôn ngữ | Vietnamese |
Định dạng | |
Dung lượng | 1.91 MB |
Tóm tắt
I.Tự động hóa quá trình sản xuất và hệ thống điều khiển
Bài viết tập trung vào việc tự động hóa các dây chuyền sản xuất hiện đại, đặc biệt nhấn mạnh vai trò của hệ thống điều khiển tự động trong việc nâng cao chất lượng sản phẩm và hiệu quả kinh tế. Việc ứng dụng công nghệ PLC (Programmable Logic Controller) và các bộ điều khiển khác như PID là trọng tâm, giải quyết các vấn đề liên quan đến thu thập, xử lý thông tin và ra quyết định chính xác, kịp thời. Hệ thống điều khiển quá trình được phân cấp, mô tả rõ ràng vai trò của con người và máy móc trong quá trình vận hành. Các hệ thống này cần đảm bảo tính chính xác cao để tránh tổn thất kinh tế và kỹ thuật. Nghiên cứu đề cập đến việc tối ưu hóa quá trình, giảm sức lao động và nâng cao năng suất.
1. Tổng quan về tự động hóa trong sản xuất công nghiệp
Đoạn mở đầu nhấn mạnh tầm quan trọng của công nghiệp hóa, hiện đại hóa đất nước, trong đó tự động hóa đóng vai trò then chốt. Tự động hóa được xem là giải pháp tối ưu để sản xuất hàng loạt sản phẩm chất lượng cao, tăng khả năng cạnh tranh trên thị trường quốc tế. Tuy nhiên, quá trình tự động hóa đi kèm với sự gia tăng mạnh mẽ lượng thông tin trao đổi giữa người và máy, giữa các máy móc với nhau. Điều này đòi hỏi hệ thống điều khiển phải xử lý một lượng thông tin khổng lồ, bao gồm cả thông tin kỹ thuật và kinh tế (chủng loại, thông số kỹ thuật, giá cả vật tư, thị trường...). Việc thu thập và xử lý thông tin chính xác, kịp thời là yếu tố quyết định đến sự thành công của quá trình sản xuất, quyết định sai lầm sẽ dẫn đến thiệt hại về kinh tế, kỹ thuật và uy tín. Do đó, việc ứng dụng các công nghệ hiện đại như điện tử, tin học, và cơ khí chính xác trong tự động hóa là điều cần thiết để đáp ứng yêu cầu ngày càng cao của ngành công nghiệp.
2. Phân cấp hệ thống điều khiển tự động và hệ thống điều khiển quá trình
Bài viết phân tích và làm rõ sự khác biệt giữa hệ thống điều khiển tự động (Automatic control system) và hệ thống điều khiển tự động hóa quá trình (Process control system). Hệ thống điều khiển tự động hoạt động hoàn toàn tự động theo chương trình đã được cài đặt sẵn, con người chỉ có vai trò khởi động hệ thống. Các thiết bị thuộc loại này bao gồm bộ điều khiển, bộ điều chỉnh PID, PLC, mạch rơ le, và contactor, thường làm việc ở cấp điều khiển 2. Ngược lại, hệ thống điều khiển tự động hóa quá trình tích hợp con người vào một phần quan trọng của hệ thống. Con người tham gia vào việc hoạch định mục tiêu, ra quyết định quan trọng, và thường xuyên trao đổi thông tin với máy móc. Hệ thống này hoạt động ở cấp điều khiển 3 và 4. Bài viết nhấn mạnh vai trò của con người trong việc đảm bảo hệ thống đạt được mục tiêu đề ra, và sự chính xác trong việc thu thập thông tin để đưa ra quyết định đúng đắn. Việc thiếu chính xác trong thông tin và năng lực hạn chế của người vận hành có thể gây ra hậu quả nghiêm trọng về kinh tế và kỹ thuật.
3. Mô tả hệ thống tự động điều khiển quá trình sản xuất mẫu
Bài viết trình bày chi tiết một ví dụ minh họa về hệ thống tự động điều khiển quá trình sản xuất, tập trung vào các trạm chính: trạm cấp phôi, trạm kiểm tra và trạm gia công. Quá trình cấp phôi được thực hiện bằng cách sử dụng xilanh khí nén và cánh tay robot hút chân không để di chuyển phôi từ ngăn chứa đến trạm kiểm tra. Ngăn chứa phôi được thiết kế dạng hình trụ, có khả năng chứa một lượng phôi nhất định, tùy thuộc vào yêu cầu của quá trình sản xuất. Trạm gia công sử dụng đĩa quay điều khiển bằng động cơ một chiều để định vị và gia công phôi. Sau khi gia công, sản phẩm được chuyển đến trạm lưu trữ và được cánh tay robot phân loại vào các thùng chứa khác nhau theo màu sắc và chủng loại. Bài viết chỉ ra các nhược điểm của hệ thống truyền thống, bao gồm việc đấu nối, lắp đặt phức tạp, tốn thời gian, hiệu quả thấp, và khó khăn trong việc sửa chữa, bảo trì. Chính những nhược điểm này đã thúc đẩy nghiên cứu và phát triển các giải pháp tự động hóa hiện đại hơn.
II.Ứng dụng PLC trong điều khiển tự động
Phần này trình bày về PLC, một thiết bị trung tâm trong hệ thống tự động hóa. Từ sự ra đời của PLC vào năm 1968 (General Moto, Mỹ) cho đến nay, PLC đã được cải tiến đáng kể với khả năng chống nhiễu cao và nhiều ưu điểm khác. Các hãng sản xuất PLC hàng đầu thế giới như Omron, Mitsubishi, Hitachi, ABB, Siemens được nhắc đến. Cấu trúc của PLC bao gồm CPU, hệ điều hành, bộ nhớ và các cổng vào/ra. Bài viết giải thích các vùng nhớ trong PLC (như I, L, DB) và cách thức hoạt động của chúng, bao gồm cả việc xử lý ngắt (interrupt). Các ngôn ngữ lập trình PLC như LAD, FBD, STL cũng được đề cập đến, đặc biệt là các lệnh cơ bản trong ngôn ngữ STL.
1. Lịch sử và sự phát triển của PLC
Phần này đề cập đến sự ra đời của PLC vào năm 1968 bởi công ty General Moto (Mỹ), đánh dấu một bước ngoặt quan trọng trong công nghệ điều khiển tự động. Ban đầu, hệ thống PLC còn khá đơn giản và cồng kềnh, gây khó khăn cho người sử dụng. Tuy nhiên, qua nhiều năm phát triển và cải tiến, PLC đã khắc phục được những nhược điểm ban đầu, trở thành một bộ điều khiển linh hoạt, đáng tin cậy với khả năng chống nhiễu cao. Hiện nay, nhiều hãng sản xuất PLC nổi tiếng trên thế giới cùng phát triển song hành, như Omron, Mitsubishi, Hitachi, ABB, và Siemens, mỗi hãng có những thế mạnh riêng đáp ứng nhu cầu đa dạng của các ngành công nghiệp khác nhau. Mặc dù có sự khác biệt về một số tính năng, nhưng các PLC đều dựa trên cùng một nguyên lý cơ bản.
2. Cấu trúc và chức năng của PLC
Để thực hiện chức năng điều khiển, PLC được cấu tạo tương tự như một máy tính, bao gồm bộ vi xử lý (CPU), hệ điều hành, bộ nhớ để lưu trữ chương trình điều khiển và dữ liệu, cũng như các cổng vào/ra để giao tiếp với môi trường bên ngoài. Ngoài ra, PLC còn tích hợp các bộ đếm thời gian (Timer), bộ đếm xung (Counter), và các hàm chuyên dụng khác, tạo nên tính linh hoạt cao. Bài viết mô tả các vùng nhớ quan trọng trong PLC, bao gồm vùng I (Process Input Image) dùng làm bộ đệm dữ liệu đầu vào số, vùng L (Local Data block) lưu trữ dữ liệu cục bộ cho các khối chương trình, và các khối hệ thống SFB (System function block) và SDB (System data block). Quá trình quét chương trình của PLC, bao gồm cả cách xử lý tín hiệu ngắt (interrupt), được giải thích để làm rõ hơn hoạt động của PLC.
3. Ngôn ngữ lập trình PLC và các lệnh cơ bản
Bài viết giới thiệu các ngôn ngữ lập trình PLC phổ biến, bao gồm LAD (Ladder Diagram) – ngôn ngữ lập trình đồ họa dễ hiểu cho những người quen thuộc với mạch điều khiển logic, và STL (Statement List) – ngôn ngữ lập trình dạng văn bản có tính linh hoạt cao. Mặc dù chương trình viết bằng STL có thể chuyển đổi sang LAD và FBD, nhưng ngược lại thì không chắc chắn do sự khác biệt trong tập lệnh. Bài viết đề cập đến các lệnh logic, lệnh dịch chuyển, lệnh so sánh, và lệnh toán học trong ngôn ngữ STL, đặc biệt là cách sử dụng các lệnh này với thanh ghi ACCU1 và ACCU2. Các lệnh rẽ nhánh điều khiển luồng chương trình (JU - lệnh nhảy vô điều kiện, LOOP - lệnh lặp) cũng được giải thích. Cuối cùng, nguyên tắc hoạt động của bộ đếm thời gian (Timer) và bộ đếm xung (Counter) trong PLC S7-300 được trình bày, bao gồm cả cách đọc giá trị đếm tức thời.
III.Cảm biến và thiết bị điều khiển trong tự động hóa
Vai trò của cảm biến trong việc giám sát và phản ánh tình trạng thực tế của quá trình sản xuất được nhấn mạnh. Bài viết đề cập đến việc sử dụng cảm biến màu sắc KEYENCE CZV21 và cảm biến tiệm cận (Proximity sensor) E2E-X1R5E1. Cảm biến encoder được giới thiệu như một thiết bị quan trọng trong các hệ thống điều khiển vòng kín, đòi hỏi độ chính xác cao. Khí nén cũng được xem xét như một nguồn năng lượng quan trọng trong nhiều ứng dụng tự động hóa.
1. Vai trò của cảm biến trong hệ thống điều khiển tự động
Trong các dây chuyền sản xuất tự động, cảm biến đóng vai trò cực kỳ quan trọng. Chúng phản ánh trạng thái thực tế của các cơ cấu chấp hành, giúp hệ thống điều khiển xác định xem quá trình công nghệ đang diễn ra đúng hay sai. Do đó, việc nghiên cứu và phát triển các loại cảm biến với nhiều tính năng, đặc biệt là khả năng thông minh và kết nối truyền thông, đang được chú trọng để nâng cao hiệu quả giám sát và điều khiển. Cảm biến ngày càng được tích hợp nhiều tính năng thông minh và khả năng kết nối truyền thông, giúp giám sát và điều khiển hệ thống tốt hơn.
2. Giới thiệu về cảm biến màu sắc KEYENCE CZV21 và cảm biến tiệm cận
Bài viết giới thiệu hai loại cảm biến cụ thể được sử dụng trong hệ thống: cảm biến màu sắc KEYENCE CZV21 và cảm biến tiệm cận không tiếp xúc. Cảm biến CZV21 hoạt động dựa trên nguyên tắc phát và thu ánh sáng, nhận biết màu sắc và hiển thị kết quả bằng số màu đỏ trên giao diện. Cảm biến này thuộc dòng sản phẩm cảm biến màu sắc của hãng KEYENCE. Bên cạnh đó, tài liệu cũng đề cập đến cảm biến tiệm cận không tiếp xúc Proxymity loại E2E-X1R5E1, nhưng không đi sâu vào chi tiết hoạt động của loại cảm biến này.
3. Cảm biến encoder và ứng dụng trong điều khiển vòng kín
Cảm biến encoder được giới thiệu như một loại cảm biến quan trọng trong các hệ thống điều khiển vòng kín, đặc biệt là trong các hệ thống truyền động đòi hỏi độ chính xác cao. Cảm biến này mã hóa tốc độ chuyển động của cơ cấu chấp hành dưới dạng xung, gửi tín hiệu về cho bộ điều khiển hoặc thiết bị hiển thị khác, ví dụ như bộ đếm. Việc sử dụng cảm biến encoder giúp cho hệ thống điều khiển có thể phản hồi chính xác và kịp thời, đảm bảo chất lượng và độ chính xác của quá trình sản xuất. Điều này cho thấy tầm quan trọng của cảm biến encoder trong việc đảm bảo độ chính xác của hệ thống điều khiển.
4. Khí nén trong hệ thống điều khiển tự động
Bài viết đề cập đến vai trò của khí nén trong hệ thống điều khiển tự động. Mặc dù năng lượng điện đã phát triển mạnh mẽ, khí nén vẫn giữ một vị trí quan trọng, không thể thay thế trong một số lĩnh vực cụ thể. Từ thế kỷ 17, với những đóng góp của các nhà bác học như Blaise Pascal, Denis Papin, và Otto von Guerike, khí nén đã được ứng dụng rộng rãi trong nhiều ngành công nghiệp. Trong thời kỳ cách mạng công nghiệp, khí nén được sử dụng nhiều trong điều khiển (phun sơn, gá kẹp chi tiết...) và truyền động (máy vặn vít, motor khí nén, máy khoan...). Khí nén được sử dụng như một tín hiệu tác động, cùng với các tín hiệu khác như điện, lò xo, hoặc tác động bằng tay. Các phần tử xử lý tín hiệu khí nén, như van logic AND, OR, van một chiều, và van tiết lưu, cũng được nhắc đến.
IV.Điều khiển động cơ một chiều và thiết bị hỗ trợ
Phần này tập trung vào động cơ một chiều, một loại động cơ được sử dụng rộng rãi trong điều khiển tốc độ chính xác. Bộ điều khiển Mentor II (Control Techniques) được giới thiệu như một giải pháp hiện đại cho việc điều khiển động cơ một chiều, với khả năng điều khiển, giám sát, bảo vệ và truyền thông mạnh mẽ. Các thông số kỹ thuật quan trọng của Mentor II như dải dòng điện ra (25A - 1850A) được nêu ra. Ngoài ra, bài viết còn đề cập đến việc sử dụng biến tần Fuji, một thiết bị quan trọng trong việc điều chỉnh tốc độ động cơ xoay chiều. Việc cài đặt và vận hành các thiết bị này được tóm tắt ngắn gọn.
1. Động cơ điện một chiều Ưu điểm nhược điểm và ứng dụng
Động cơ điện một chiều vẫn được sử dụng rộng rãi trong các hệ thống điều khiển tự động, đặc biệt là những ứng dụng đòi hỏi điều chỉnh tốc độ chính xác cao và mômen lớn. Dải công suất của động cơ một chiều rất đa dạng, từ vài W đến hàng MW, đáp ứng được nhiều nhu cầu khác nhau trong công nghiệp, ví dụ như cán thép, hầm mỏ, và giao thông vận tải. Tuy nhiên, động cơ một chiều cũng có những nhược điểm như giá thành cao, sử dụng nhiều kim loại màu, và việc bảo quản cổ góp phức tạp. Việc đánh lửa giữa chổi than và cổ góp cũng là một vấn đề thường gặp, đòi hỏi các biện pháp khắc phục tương đối khó khăn. Mặc dù vậy, những ưu điểm về khả năng điều chỉnh tốc độ khiến động cơ một chiều vẫn giữ vai trò quan trọng trong nhiều ngành công nghiệp.
2. Cấu tạo và nguyên lý hoạt động của động cơ một chiều
Động cơ một chiều gồm hai phần chính: phần tĩnh và phần động. Dây quấn phần ứng là bộ phận tham gia trực tiếp vào quá trình biến đổi năng lượng điện từ, được bố trí trên các rãnh của lõi thép phần ứng. Cổ góp, được coi là bộ chỉnh lưu cơ khí, đóng vai trò đổi chiều dòng điện. Cổ góp được tạo thành từ các phiến góp đồng, được cách điện với nhau bởi mica. Các phương pháp kích từ, bao gồm kích từ độc lập, kích từ nối tiếp, và kích từ hỗn hợp (kết hợp nối tiếp và song song), cũng được đề cập. Trong quá trình hoạt động, cần chú ý đến các chế độ làm việc như khởi động, chế độ làm việc chính, và chế độ hãm để đảm bảo động cơ hoạt động ổn định với tải. Việc điều chỉnh tốc độ động cơ một chiều có thể thực hiện thông qua hai phương pháp cơ bản.
3. Giới thiệu bộ điều khiển Mentor II cho động cơ một chiều
Trong công nghiệp hiện đại, việc điều khiển động cơ một chiều đòi hỏi độ chính xác cao về tốc độ và mômen. Bộ điều khiển Mentor II của hãng Control Techniques là một giải pháp đáp ứng được những yêu cầu này. Mentor II là bộ điều khiển số sử dụng vi xử lý, có dải dòng ra lớn (25A đến 1850A), tích hợp đầy đủ các chức năng điều khiển, giám sát, bảo vệ, và truyền thông nối tiếp. Việc lựa chọn các thiết bị hỗ trợ như cầu chì, cáp cấp, và phương pháp lắp đặt đúng tiêu chuẩn của nhà sản xuất là rất quan trọng. Việc cài đặt thông số có thể thực hiện trực tiếp trên bộ điều khiển hoặc thông qua phần mềm Mentorsoft, giúp việc cấu hình dễ dàng hơn so với việc sử dụng bàn phím. Phần mềm CTcope tích hợp sẵn trong Mentor II giúp người dùng quan sát dễ dàng các thông số như tốc độ, dòng điện, và mômen, đảm bảo quá trình điều khiển đạt hiệu quả tối ưu.